Segells mecànicstenen un paper molt important per evitar les fuites per a moltes indústries diferents. A la indústria marina hi hasegells mecànics de bomba, segells mecànics d'eix rotatiu. I a la indústria del petroli i el gas hi hasegells mecànics de cartutx,segells mecànics dividits o segells mecànics de gas sec. A les indústries de l'automòbil hi ha segells mecànics d'aigua. I a la indústria química hi ha segells mecànics de mesclador (segells mecànics d'agitador) i segells mecànics de compressor.
Depenent de les diferents condicions d'ús, cal una solució de segellat mecànic amb materials diferents. Hi ha molts tipus de materials utilitzats en elsegells mecànics d'eix com ara segells mecànics de ceràmica, segells mecànics de carboni, segells mecànics de carbur de silicona,Segells mecànics SSIC iSegells mecànics TC.
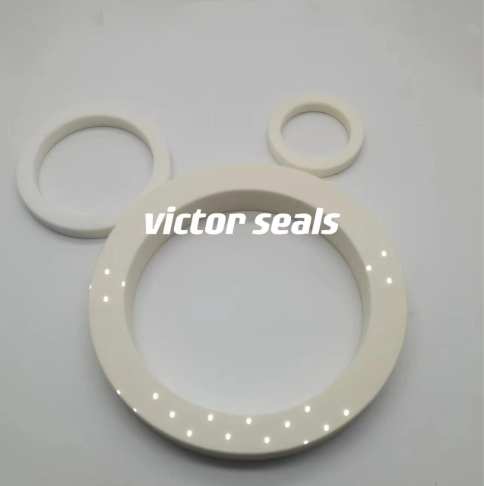
Segells mecànics ceràmics
Els segells mecànics ceràmics són components crítics en diverses aplicacions industrials, dissenyats per evitar fuites de fluids entre dues superfícies, com ara un eix giratori i una carcassa estacionària. Aquests segells són molt valorats per la seva excepcional resistència al desgast, resistència a la corrosió i capacitat per suportar temperatures extremes.
La funció principal dels segells mecànics ceràmics és mantenir la integritat dels equips evitant la pèrdua de fluids o la contaminació. S'utilitzen en nombroses indústries, com ara el petroli i el gas, el processament químic, el tractament d'aigües, els productes farmacèutics i el processament d'aliments. L'ús generalitzat d'aquests segells es pot atribuir a la seva construcció duradora; estan fets de materials ceràmics avançats que ofereixen característiques de rendiment superiors en comparació amb altres materials de segellat.
Els segells mecànics ceràmics consten de dos components principals: un és una cara estacionària mecànica (normalment feta de material ceràmic) i l'altre és una cara rotativa mecànica (normalment construïda amb grafit de carboni). L'acció de segellat es produeix quan ambdues cares es pressionen juntes mitjançant una força de ressort, creant una barrera eficaç contra les fuites de fluids. A mesura que l'equip funciona, la pel·lícula lubricant entre les cares de segellat redueix la fricció i el desgast alhora que manté un segellat hermètic.
Un factor crucial que diferencia els segells mecànics ceràmics d'altres tipus és la seva excepcional resistència al desgast. Els materials ceràmics posseeixen excel·lents propietats de duresa que els permeten suportar condicions abrasives sense danys significatius. Això resulta en segells més duradors que requereixen menys freqüència de substitució o manteniment que els fets de materials més tous.
A més de la resistència al desgast, les ceràmiques també presenten una estabilitat tèrmica excepcional. Poden suportar altes temperatures sense patir degradació ni perdre la seva eficiència de segellat. Això les fa adequades per al seu ús en aplicacions d'alta temperatura on altres materials de segellat podrien fallar prematurament.
Finalment, els segells mecànics ceràmics ofereixen una excel·lent compatibilitat química, amb resistència a diverses substàncies corrosives. Això els converteix en una opció atractiva per a les indústries que treballen habitualment amb productes químics agressius i fluids agressius.
Els segells mecànics ceràmics són essencialssegells de componentsdissenyats per evitar fuites de fluids en equips industrials. Les seves propietats úniques, com ara la resistència al desgast, l'estabilitat tèrmica i la compatibilitat química, els converteixen en una opció preferida per a diverses aplicacions en múltiples indústries.
propietat física ceràmica | ||||
paràmetre tècnic | unitat | 95% | 99% | 99,50% |
Densitat | g/cm3 | 3.7 | 3,88 | 3.9 |
Duresa | HRA | 85 | 88 | 90 |
Taxa de porositat | % | 0,4 | 0,2 | 0,15 |
Resistència fractural | MPa | 250 | 310 | 350 |
Coeficient de dilatació tèrmica | 10(-6)/K | 5.5 | 5.3 | 5.2 |
Conductivitat tèrmica | W/MK | 27,8 | 26,7 | 26 |
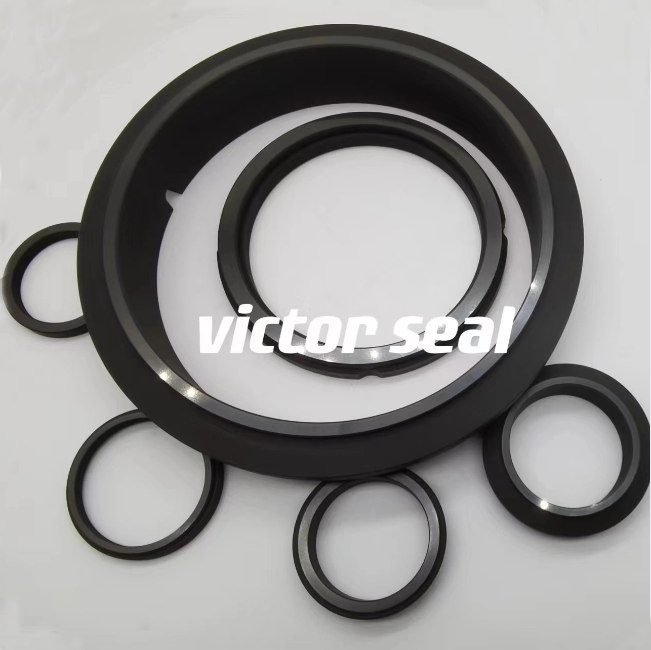
Segells mecànics de carboni
El segell mecànic de carboni té una llarga història. El grafit és una isoforma de l'element carboni. El 1971, els Estats Units van estudiar el material de segellat mecànic de grafit flexible amb èxit, que va resoldre el problema de les fuites de les vàlvules d'energia atòmica. Després d'un processament profund, el grafit flexible es converteix en un excel·lent material de segellat, que es transforma en diversos segells mecànics de carboni amb l'efecte de segellar components. Aquests segells mecànics de carboni s'utilitzen en les indústries química, petroliera i elèctrica, com ara els segells de fluids d'alta temperatura.
Com que el grafit flexible es forma per l'expansió del grafit expandit després d'una temperatura elevada, la quantitat d'agent intercalant que queda al grafit flexible és molt petita, però no completament, de manera que l'existència i la composició de l'agent intercalant tenen una gran influència en la qualitat i el rendiment del producte.
Selecció del material de la cara del segell de carboni
L'inventor original va utilitzar àcid sulfúric concentrat com a oxidant i agent intercalant. Tanmateix, després d'aplicar-lo al segellat d'un component metàl·lic, es va descobrir que una petita quantitat de sofre que quedava al grafit flexible corroïa el metall de contacte després d'un ús a llarg termini. Tenint en compte aquest punt, alguns estudiosos nacionals han intentat millorar-lo, com ara Song Kemin, que va triar àcid acètic i àcid orgànic en lloc d'àcid sulfúric. L'àcid, lent en àcid nítric i baixant la temperatura a temperatura ambient, es va fer a partir d'una barreja d'àcid nítric i àcid acètic. Utilitzant la barreja d'àcid nítric i àcid acètic com a agent d'inserció, es va preparar el grafit expandit sense sofre amb permanganat de potassi com a oxidant i s'afegia lentament àcid acètic a l'àcid nítric. Es redueix la temperatura a temperatura ambient i es fa la barreja d'àcid nítric i àcid acètic. A continuació, s'afegeixen el grafit natural en escates i el permanganat de potassi a aquesta barreja. Sota agitació constant, la temperatura és de 30 C. Després de 40 minuts de reacció, l'aigua es renta fins a la neutralitat i s'asseca a 50~60 C, i el grafit expandit es produeix després d'una expansió a alta temperatura. Aquest mètode no aconsegueix vulcanització si el producte pot assolir un cert volum d'expansió, per tal d'aconseguir una naturalesa relativament estable del material de segellat.
Tipus | M106H | M120H | M106K | M120K | M106F | M120F | M106D | M120D | M254D |
Marca | Impregnat | Impregnat | Fenol impregnat | Carboni d'antimoni (A) | |||||
Densitat | 1,75 | 1.7 | 1,75 | 1.7 | 1,75 | 1.7 | 2.3 | 2.3 | 2.3 |
Resistència fractural | 65 | 60 | 67 | 62 | 60 | 55 | 65 | 60 | 55 |
Resistència a la compressió | 200 | 180 | 200 | 180 | 200 | 180 | 220 | 220 | 210 |
Duresa | 85 | 80 | 90 | 85 | 85 | 80 | 90 | 90 | 65 |
Porositat | <1 | <1 | <1 | <1 | <1 | <1 | <1,5 | <1,5 | <1,5 |
Temperatures | 250 | 250 | 250 | 250 | 250 | 250 | 400 | 400 | 450 |
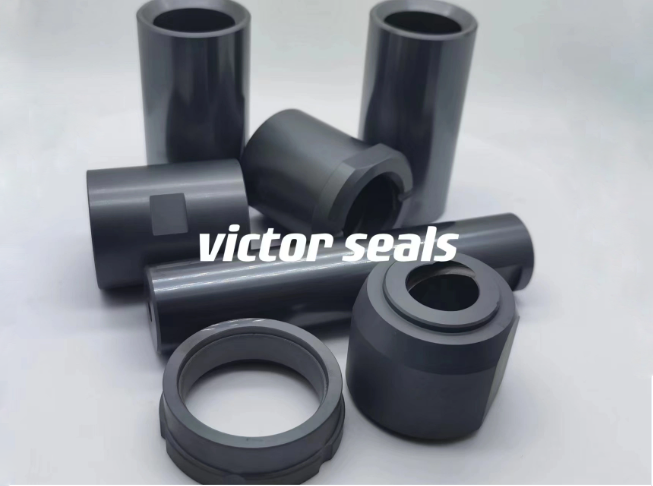
Segells mecànics de carbur de silici
El carbur de silici (SiC) també es coneix com a carborúndum, que està fet de sorra de quars, coc de petroli (o coc de carbó), estelles de fusta (que cal afegir quan es produeix carbur de silici verd), etc. El carbur de silici també té un mineral rar en la naturalesa, la morera. En les matèries primeres refractàries contemporànies de C, N, B i altres matèries primeres refractàries d'alta tecnologia sense òxid, el carbur de silici és un dels materials més utilitzats i econòmics, que es pot anomenar sorra d'acer daurat o sorra refractària. Actualment, la producció industrial xinesa de carbur de silici es divideix en carbur de silici negre i carbur de silici verd, tots dos cristalls hexagonals amb una proporció de 3,20 ~ 3,25 i una microduresa de 2840 ~ 3320 kg/m².
Els productes de carbur de silici es classifiquen en molts tipus segons els diferents entorns d'aplicació. Generalment s'utilitzen més mecànicament. Per exemple, el carbur de silici és un material ideal per a segells mecànics de carbur de silici a causa de la seva bona resistència a la corrosió química, alta resistència, alta duresa, bona resistència al desgast, baix coeficient de fricció i alta resistència a la temperatura.
Els anells de segellat SIC es poden dividir en anells estàtics, anells mòbils, anells plans, etc. El silici SiC es pot fabricar en diversos productes de carbur, com ara anells rotatius de carbur de silici, seients estacionaris de carbur de silici, casquets de carbur de silici, etc., segons els requisits especials dels clients. També es pot utilitzar en combinació amb material de grafit, i el seu coeficient de fricció és menor que el de la ceràmica d'alúmina i l'aliatge dur, de manera que es pot utilitzar en un valor fotovoltaic alt, especialment en condicions d'àcid fort i àlcali fort.
La reducció de la fricció del SIC és un dels principals avantatges d'utilitzar-lo en segells mecànics. Per tant, el SIC pot suportar el desgast millor que altres materials, cosa que allarga la vida útil del segell. A més, la reducció de la fricció del SIC disminueix la necessitat de lubricació. La manca de lubricació redueix la possibilitat de contaminació i corrosió, millorant l'eficiència i la fiabilitat.
El SIC també té una gran resistència al desgast. Això indica que pot suportar un ús continu sense deteriorar-se ni trencar-se. Això el converteix en el material perfecte per a usos que exigeixen un alt nivell de fiabilitat i durabilitat.
També es pot tornar a solapar i polir, de manera que un segell es pot restaurar diverses vegades al llarg de la seva vida útil. Generalment s'utilitza de manera més mecànica, com ara en segells mecànics, per la seva bona resistència a la corrosió química, alta resistència, alta duresa, bona resistència al desgast, baix coeficient de fricció i alta resistència a la temperatura.
Quan s'utilitza per a cares de segellat mecànic, el carbur de silici millora el rendiment, augmenta la vida útil del segellat, redueix els costos de manteniment i redueix els costos de funcionament dels equips rotatius com ara turbines, compressors i bombes centrífugues. El carbur de silici pot tenir diferents propietats segons com s'ha fabricat. El carbur de silici unit per reacció es forma unint partícules de carbur de silici entre si en un procés de reacció.
Aquest procés no afecta significativament la majoria de les propietats físiques i tèrmiques del material, però sí que limita la resistència química del material. Els productes químics més comuns que representen un problema són els càustics (i altres productes químics de pH alt) i els àcids forts, i per tant, el carbur de silici enllaçat per reacció no s'hauria d'utilitzar amb aquestes aplicacions.
Infiltrat per reacció sinteritzatcarbur de silici. En aquest material, els porus del material SIC original s'omplen en el procés d'infiltració mitjançant la crema del silici metàl·lic, de manera que apareix el SiC secundari i el material adquireix propietats mecàniques excepcionals, esdevenint resistent al desgast. A causa de la seva mínima contracció, es pot utilitzar en la producció de peces grans i complexes amb toleràncies estretes. Tanmateix, el contingut de silici limita la temperatura màxima de funcionament a 1.350 °C, i la resistència química també està limitada a un pH aproximat de 10. No es recomana l'ús del material en ambients alcalins agressius.
SinteritzatEl carbur de silici s'obté sinteritzant un granulat de SIC molt fi precomprimit a una temperatura de 2000 °C per formar enllaços forts entre els grans del material.
Primer, la xarxa s'espesseix, després la porositat disminueix i finalment els enllaços entre els grans se sinteritzen. En el procés d'aquest processament, es produeix una contracció significativa del producte, d'aproximadament un 20%.
Anell de segellat SSIC és resistent a tots els productes químics. Com que no hi ha silici metàl·lic present a la seva estructura, es pot utilitzar a temperatures de fins a 1600 °C sense afectar la seva resistència.
propietats | R-SiC | S-SiC |
Porositat (%) | ≤0,3 | ≤0,2 |
Densitat (g/cm3) | 3.05 | 3.1~3.15 |
Duresa | 110~125 (HS) | 2800 (kg/mm2) |
Mòdul elàstic (Gpa) | ≥400 | ≥410 |
Contingut de SiC (%) | ≥85% | ≥99% |
Contingut de Si (%) | ≤15% | 0,10% |
Resistència a la flexió (Mpa) | ≥350 | 450 |
Resistència a la compressió (kg/mm2) | ≥2200 | 3900 |
Coeficient d'expansió tèrmica (1/℃) | 4,5 × 10-6 | 4,3 × 10-6 |
Resistència a la calor (a l'atmosfera) (℃) | 1300 | 1600 |
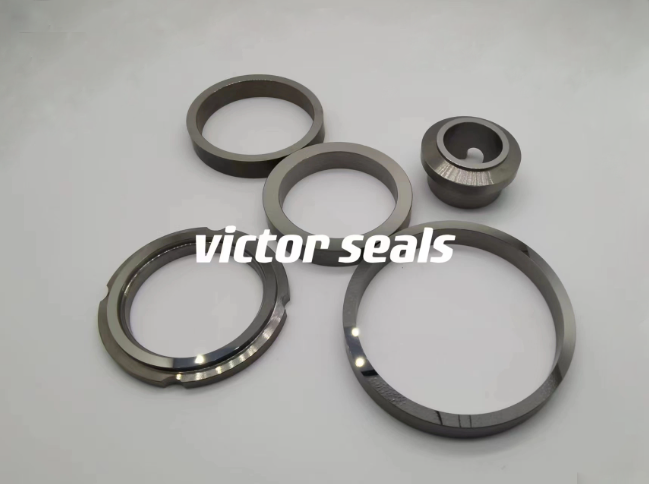
Segell mecànic TC
Els materials de carbur de tungstè tenen característiques d'alta duresa, resistència, resistència a l'abrasió i a la corrosió. Se'ls coneix com a "dents industrials". A causa del seu rendiment superior, s'han utilitzat àmpliament en la indústria militar, aeroespacial, processament mecànic, metal·lúrgia, perforació de petroli, comunicació electrònica, arquitectura i altres camps. Per exemple, en bombes, compressors i agitadors, els anells de carbur de tungstè s'utilitzen com a segells mecànics. La bona resistència a l'abrasió i l'alta duresa els fan adequats per a la fabricació de peces resistents al desgast amb altes temperatures, fricció i corrosió.
Segons la seva composició química i les seves característiques d'ús, el TC es pot dividir en quatre categories: tungstè-cobalt (YG), tungstè-titani (YT), tungstè-titani-tàntal (YW) i carbur de titani (YN).
L'aliatge dur de tungstè-cobalt (YG) està compost de WC i Co. És adequat per processar materials fràgils com ara ferro colat, metalls no ferrosos i materials no metàl·lics.
L'estelita (YT) està composta de WC, TiC i altres components. A causa de l'addició de TiC a l'aliatge, la seva resistència al desgast millora, però la resistència a la flexió, el rendiment de mòlta i la conductivitat tèrmica disminueixen. A causa de la seva fragilitat a baixa temperatura, només és adequada per al tall a alta velocitat de materials generals i no per al processament de materials fràgils.
S'afegeix tungstè, titani, tàntal (niobi) i cobalt (YW) a l'aliatge per augmentar la duresa, la resistència i la resistència a l'abrasió a altes temperatures mitjançant una quantitat adequada de carbur de tàntal o carbur de niobi. Al mateix temps, també millora la tenacitat amb un millor rendiment de tall integral. S'utilitza principalment per a materials de tall durs i tall intermitent.
La classe base de titani carbonitzat (YN) és un aliatge dur amb la fase dura de TiC, níquel i molibdè. Els seus avantatges són una alta duresa, capacitat antiadherent, antidesgast creixent i capacitat antioxidació. A una temperatura de més de 1000 graus, encara es pot mecanitzar. És aplicable a l'acabat continu d'acer d'aliatge i acer de tremp.
model | contingut de níquel (% en pes) | densitat (g/cm²) | duresa (HRA) | resistència a la flexió (≥N/mm²) |
YN6 | 5,7-6,2 | 14,5-14,9 | 88,5-91,0 | 1800 |
YN8 | 7,7-8,2 | 14,4-14,8 | 87,5-90,0 | 2000 |
model | contingut de cobalt (% en pes) | densitat (g/cm²) | duresa (HRA) | resistència a la flexió (≥N/mm²) |
YG6 | 5.8-6.2 | 14,6-15,0 | 89,5-91,0 | 1800 |
YG8 | 7,8-8,2 | 14,5-14,9 | 88,0-90,5 | 1980 |
YG12 | 11,7-12,2 | 13,9-14,5 | 87,5-89,5 | 2400 |
YG15 | 14,6-15,2 | 13.9-14.2 | 87,5-89,0 | 2480 |
YG20 | 19,6-20,2 | 13,4-13,7 | 85,5-88,0 | 2650 |
YG25 | 24,5-25,2 | 12.9-13.2 | 84,5-87,5 | 2850 |